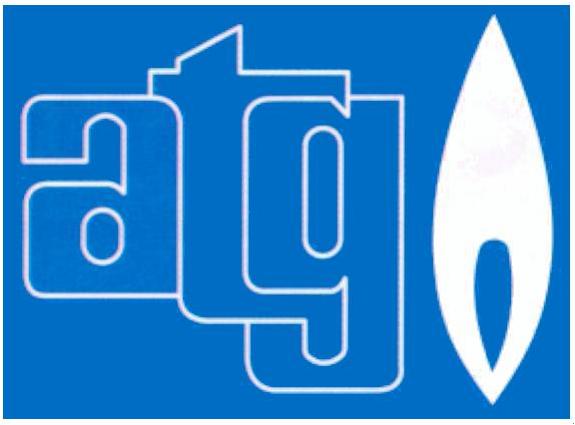
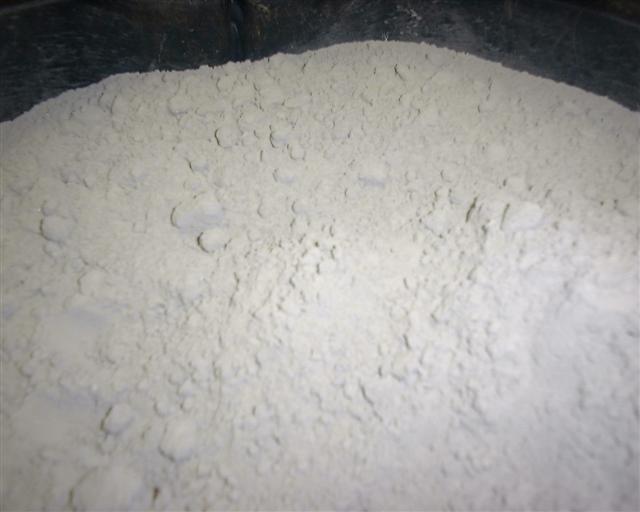
Stripper fluxes should have the following properties:
Melt at a temperature at least 100°C lower than the filler alloy solidus (correlation with solder and joined metals)
Remain stable up to the maximum temperature required (activity range)
Remain active throughout the entire soldering cycle (lifetime)
Dissolve the metal oxides of the different metals in play (choice of the type of flux)
Be sufficiently fluid, even when loaded with dissolved oxides, to be easily moved by the solder in the capillary interstices of the joint
Be easy to remove after brazing (distribution of borax, boric acid, alkali fluorides and bi-fluorides)
The surfaces intended to be brazed must be cleaned beforehand, in order to eliminate the greases and stable oxides present before and during air brazing and whose presence hinders the wetting of the braze. This requires the use of flux, which then has the role, during brazing, of forming a continuous film on the surface of the joint in order to prevent oxidation of the latter.
There is also a process for the saturation of acetylene gas with an appropriate deoxidizer carried out by passing the gas through an autofluxing device filled with the Fluxogaz liquid in order to give the usually oxidizing flame a deoxidizing power. However, this process exclusively prevents the formation of oxides on the outside of the seal and not on the inside, where a pasty flux suitable for assembly will be applied.
Certain precautions must be taken when using them.
The fluxes contain irritating and/or toxic products and must not remain in contact with the skin. Moreover, at certain temperatures, the flows are unstable and give off toxic vapors for the eyes and mucous membranes. It is therefore necessary to ventilate the workshops and soldering stations well.